Primer: Insensitive Munitions (IM)
- Jon Hawkes
- Jan 31, 2022
- 16 min read
Insensitive Munition (IM) standards make munitions, whether missiles, cannon rounds or other explosives, much safer to store, handle and use. But IM is a term that is thrown around or appended to a designation without a whole lot of clarity as to what it means. This primer attempts a rapid run through of what IM is, how its tested, how you engineer for it, and what it all means for AFVs anyway.
Contents
Start simple - what is IM? IM is a classification that tries to achieve a state where unanticipated stimuli will not produce an explosive yield in a munition - accidental or inadvertent initiation of charges is not possible and any effect is minimised to prevent significant collateral damage. This is whether during manufacture, handling, storage, transport, usage or disposal.
"Not 'safe', just less violent" Munitions Safety Information Analysis Center (MSIAC)
In simple terms, the goal is that nothing but an intentional initiation when firing a round will cause that rounds to detonate. There are varying levels of compliance - you have to accept you're dealing with lumps of propellant and explosive, so the scale runs from burning to detonating. IM engineering and compliance is about reducing the reaction down that scale as far as possible.

Not all stimuli are equal, and the responses to them may vary significantly too, so IM certification conducts a number of tests and grades against each, resulting in a matrix (called the IM Signature) of how a particular round performs. The test is by no means a simple all pass or all fail concept, and the response to be graded a pass can vary depending on the ammunition type and usage case, though a baseline default does exist.
IM Tests
The IM test profile covers six stimulus events, recording the reaction to each distinctly:
1. Fast Cookoff (FCO) simulates the round being in direct contact exposure with a fuel fire, simulating events like an aircraft fire on a flight deck, or a vehicle fire following an accident or destruction by hostile fire. The round is directly exposed the heat generated within the incandescent flame envelope of a large liquid hydrocarbon fire. STANAG 4240 directs that the test be conducted by suspending the round 1 m above a burning fuel fire and left there until the munition reacts.
"In the standard [FCO] liquid fuel/external fire test, the test specimen is surrounded by fuel rich flames from a large open hearth containing liquid fuel. The large horizontal dimensions of the hearth ensure that the flames are fuel rich and hence heat transfer to the test specimen is approximately 90% radiative. ... The fuel fire tests are designed only to simulate the most intense heating conditions likely to be created in a hydrocarbon fuel fire. They do not, however, simulate a particular in-service or accident scenario. Where it is determined that only packaged items will be exposed to accidental liquid fuel fires in the service environments (including storage, transport and processing), tests should be conducted with the test item in the packaged configuration." STANAG 4240 FAST HEATING MUNITION TEST PROCEDURES

2. Slow Cookoff (SCO) simulates the round being slowly heated due to a fire in an adjacent magazine or storage area. The round is gradually heated (6°F/hr) until a reaction is observed. SCO tests can actually have more violent responses than FCO, because the energetic material in a round (especially explosives) can pass hazardous temperatures without initiation, and so once the round is initiated it can respond very violently. STANAG 4382 covers the test criteria, which see the round is placed in a 'disposable' fan oven and heated uniformly.
"The test item must be to the full production standard, although non-explosive sections of the item need only be geometrically and thermally representative. For all-up rounds that contain more than one major energetic component (such as rocket motors and warheads), the energetic components may be tested either individually or as an all-up round. ... The oven should be constructed so as to provide the least possible confinement for any reactions that occur and it should have a window to permit video coverage. ... Using the facility, test set-up, and instrumentation specified in the test plan, subject the test item to gradually increasing temperatures at a rate of 6° F/hour, until a reaction occurs, and record its reaction as a function of time and temperature. STANAG 4382 SLOW HEATING TEST PROCEDURES FOR MUNITIONS

3. Bullet Impact (BI) simulates the round being impacted and penetrated by small arms fire, which is actually quite a demanding test in the form of a three round burst of 12.7 mm (0.5") armour piercing (AP) projectiles. STANAG 4241 gives us the test criteria which fire at two locations on the round. As the STANAG explains, the test cannot simulate the vast range of ways a round could be impacted by a projectile and so seeks to find the two most stressing tests to create a worst case scenario.
"The test item shall normally be positioned with Its longest axis horizontal on a suitable stand at a height to facilitate ease of testing. ... Two tests are required, one aiming at the largest explosive component, and the other aimed at the most shock-sensitive explosive component. The target area shall be a 5cm circle. For bullet impacts, a range of approximately 20 - 30 m to the target (sufficient for bullet stabilization) is acceptable. The impact velocity must be adjusted to 850 +/- 20 m/s and the rate of fire shall be equivalent to 600 +/-50 rds/minute." STANAG 4241 BULLET IMPACT MUNITION TEST PROCEDURES
4. Fragment Impact (FI) simulates the round being impacted by high velocity fragments from a warhead, bomb or artillery shell. STANAG 4496 is our friend here, and is very specific compared to some of the earlier tests, with a lot of direction on fragment geometry and ballistics. The round is packaged as it would be stored or transported, and so the test is as much a test of the protection of the round as the characteristics of the round itself. As always, the result is recorded and assessed against the pass criteria.
"The fragment to be fired at the test item must be a right circular cylinder with a conical tipped nose with a mass of 18.6 grams (specific details provided in the STANAG). Two test procedures are identified for this test: a standard procedure where the fragment impact velocity is 8300 +/- 300 fps; or an alternate procedure where the fragment impact velocity is 6000 +/- 200 fps (if deemed credible by a threat hazard analysis). The point of impact of the fragment will be chosen in order to generate the worst reaction: one test is conducted with impact in the center of the largest presented area of energetic material or component and the second in the most shock sensitive region." STANAG 4496 FRAGMENT IMPACT, MUNITIONS TEST PROCEDURE
5. Shaped Charge Jet Impact (SCJI) simulates initiation due to a direct hit from a shaped charge jet from weapons like rocket propelled grenades, anti tank missiles, land mines, high end IEDs or bomblets. STANAG 4526 lays out the procedures and test the round in transport and 'tactical' conditions, any shielding or protective measures present in either condition are allowed.
"The test is most appropriate for systems containing materials having a detonation failure diameter significantly larger than the jet diameter. Systems containing materials with small failure diameters, including most warheads, will normally fail this test. Consider this when determining whether or not to conduct the test. ... The test may also be unnecessary if it can be reliably shown that the detonation failure diameter of the energetic material Is larger than the diameter of the munition (so that a detonation cannot be sustained), and if the threat hazard assessment Indicates that reactions less severe than [full or partial detonation] are not a concern." STANAG 4526 SHAPED CHARGE JET MUNITION TEST PROCEDURE
6. Sympathetic Reaction (SR) tests the response when an adjacent round detonates to see if a chain reaction of responses will propagate through a magazine or other storage arrangement. STANAG 4396 lays out the criteria, which place the rounds in the in-service storage situation and then detonate one to see how the remaining rounds respond.
"The purpose of this test to: subject one or more acceptor munitions to the effects of the worst case credible reaction of an identical donor munition, in the in-service situation assessed to be the most likely to result in sympathetic reaction; determine the sympathetic reaction sensitivity of munitions; and provide an indication of the effectiveness of safety barriers or other devices used to separate either single, packaged, or multiple packages of munitions. The test is generally not required for IM if the item will not detonate. The test items should be in their storage/transport configuration, but in the smallest configuration (smallest individual package) offered. The test items (donor and acceptors) must be to the full production standard, although non-explosive sections of the items need only be geometrically and thermally representative. In the case of a storage stack, the donor munition should be surrounded by the acceptor munitions, with similar but inert munitions providing the outer containment. Where protection devices are used with the objective of reducing the likelihood of sympathetic reaction, they shall be included in the test configuration. Two tests shall be performed – one with confinement and one without. Any confinement should represent that of a typical storage confinement." STANAG 4396 SYMPATHETIC REACTION TEST PROCEDURES FOR MUNITIONS
Responses
Responses to these tests are recorded against a range of factors and assessment workflows, but essentially end up recorded as one of six reactions, which are defined in AOP-39 POLICY FOR INTRODUCTION AND ASSSESSMENT OF INSENSITIVE MUNITION (IM).
Type I: Detonation. The worst case response sees the energetic material detonate with 'prompt consumption of all EM [Energetic Material] once the reaction starts". The case will be rapidly deformed and experience high velocity fragmentation, and a shock wave (of 1,800 m/s to 9,000 m/s) will be produced in conformity with that expected from an intentional initiation of the munition. In general terms, detonation is relatively unlikely to occur from heat alone, and requires an initiation by a shock wave or electric impulse. A detonation result is always a fail against any IM test.
Type II: Partial detonation. Is a reduced version of Type I, with the differentiation being that not all EM is consumed (resulting in scattered or only burned EM being found at the test location), the case may not be entirely deformed, and the shockwaves will be below the threshold of that expected of an intentional detonation. The result is still very violent, and Type I and II are usually grouped into a Type I/II failure result.
Type III: Explosion. An explosion is a lower order event than a detonation, as it is a subsonic event, but faster than a Type IV deflagration response. An explosion is generally an inherently unstable intermediate phenomena that is not clearly accounted for. Most or all of the EM will be consumed, and the case with be extensively fractured but without evidence of the higher shear rate fragmentation commensurate with a detonation. There will not be a shock wave as there would with the more violent detonation response.
Type IV: Deflagration. Deflagration is essentially very rapid burning, but still two to three orders of magnitude lower than a detonation. Cases may rupture but would not fragment beyond a few large pieces, and though there would be a pressure wave, there would not be a shock wave.
Type IV can be divided into Type IV(f), Type IV(p) and Type IV (fp), referring to a deflagration with fragmentation, a deflagration that initiates some propulsion of the round (generally by inadvertent ignition of a propellant), or both. This differentiation is important as the effects of fragmentation versus propulsion are totally different in nature and risk.
Type V: Burning. Burning is a sequence of chemical reactions, with material being brought to ignition point in receding surface layers by means of radiated or conducted heat. Essentially, the material burns away from the outside. This is a key difference from the more dramatic detonations and explosions - there is no shock wave travelling through the material and so the rate of burn is limited and only occurs at the surface of the material.
Type VI: No sustained reaction. Essentially means nothing significant happens. There may be isolated and momentary effects, but no reaction is sustained in the EM and the casing of the round has no effect other than that expected of a comparable inert item (i.e. the case may be damaged, but has not fragmented or warped due to the EM reacting or changing).
The IM Signature
So, once you've tested the different versions and configurations of your munition in the six exciting ways above, and recorded which of the six degrees of reaction occur, you can build out a matrix, which is referred to as the IM Signature.
Generally, they will then be colour coded with traffic lights for pass (green) and fail (yellow/red, with yellow denoting only one level away from a pass, and red at least two levels away). Below is an example of an IM Signature for the IRIS-T missile, with the distinct elements of the weapon tested separately.

You can also rack up a range of munitions that might be carried on a platform and arrange them in a similar grid to give a whole platform view of IM risk, this example a genericised example and not for any explicit real world equipment.

This illustrates quite well that IM is not a simple pass or fail concept, it is very nuanced and contextual to the round, the test, and the application. Something that is 'IM compliant' may only tick one box, or all of them. How well it passes may vary.
Pass/fail criteria vary by test type, national standards and the application, but in general terms are separated into two groups. SCJI and SR are much more stressing events that are near impossible to prevent from having a dramatic response by the EM, and in recognition of this the pass level is lower and the focus is on preventing detonation rather than expecting to achieve a low rate burn.
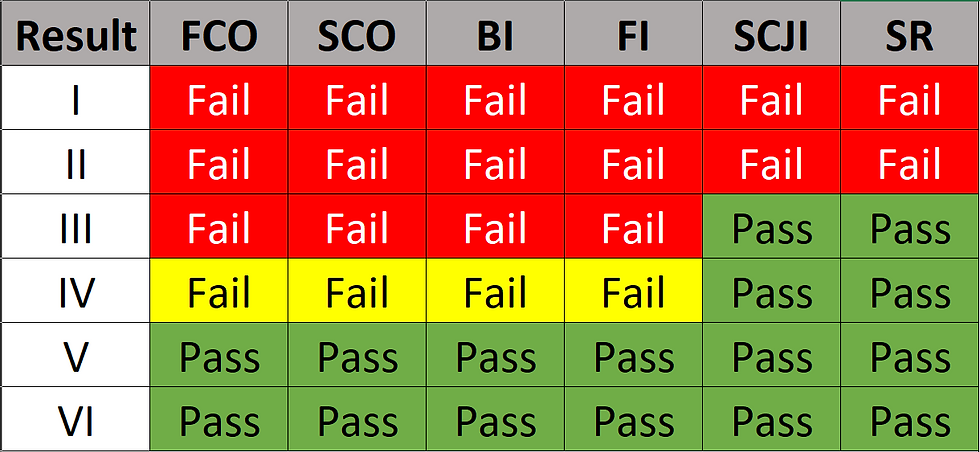
There are a few national peculiarities to IM testing and evaluation. The US has an additional test laid out in MIL-STD 2105C to cover hot spalling, where a SCJ is fired through a steel plate so that spalling is projected onto rounds beneath them. France uses the MURAT (Munitions à Risques Atténués) standards that break fragmentation tests into light and heavy weight fragmentation, and adds electrical and drop tests., with three standards that can vary in pass requirement and test inclusion. NATO writ large and the UK simply adhere to STANAG 4439.

Engineering for IM
Making something packed full of energetic material not do energetic things when exposed to extremes of heat and physical impact is quite an engineering challenge, which is why IM is still difficult to achieve and varies in its success. In general terms, the munition, whether a missile or round of ammunition, need to be reviewed and engineered with a systems approach, rather than any specific single component being changed.
EM Selection and design
Propellants and explosive compositions can be adjusted to utilise materials that are inherently less sensitive to shock and thermal decomposition. The binder ingredient is often a key element in IM design. Using binders that are less likely to shatter under shock forces will reduce the breakup of the material, and thus reduce the surface area available for a reaction to propagate over. Similarly binders that maintain good integrity under thermal loading can prevent explosive materials from clumping which would increase the likelihood of a high order response. The physical structure and manufacturing processes of materials can also be adjusted - smaller particles have been shown to reduce shock sensitivity, for example.
It is not uncommon for IM adjustments to reduce the efficacy of the EM as a result, and so further adjustments have to be made to maintain the material's performance under intentional initiation. Fixing this shortcoming is achieved by reducing the proportion of inert components of the EM, or replacing some inert components with energetic ones. This needs to be carefully balanced so as to not cause new problems under IM test conditions.
Munition design
A key factor in EM rising up the results table towards a detonation is how confined the material is. An EM that just burns in the open might detonate when suitably confined. Given the designer wants the munition to burn fiercely or detonate when intentional, getting it to not do this the rest of the time is difficult - it is confined in a casing and structured to do exactly what the IM engineer is asking it not to. The confinement of the casing inherently prevents gases from escaping quickly and raises pressure quickly towards a high order result.

Mitigating this pressure build-up is typically achieved by passive and active venting. Passive reflects vent paths, usually covered, that are engineered to open in the event of a sudden pressure increase. In an AFV domain this is most commonly seen in blow off panels in ammunition compartments to prevent a detonation and safely vent the pressure away from the vehicle. Active venting is more common in missiles and large warheads, where the EM create a path in the event of it initiating improperly.
Finally where possible EM can be designed to be below the critical diameter. The critical diameter (also called the failure diameter) is the minimum diameter of an EM cylinder which cam sustain a high order steady-state detonation. If the material is below this size it cannot detonate, useful for propellant and propulsion materials. Beyond propellant it is rarely a factor that can be used, as the critical diameter for most EM is <5 mm.
Packaging and storage design
The next part is to move out from the munition itself and see how its environment can be reengineered to help it in the event of an accident or attack. How rounds are packaged and how they are stored within the vehicle can have a significant impact. Ultimately the designer is seeking to limit the amount of energy that can be imparted into the munition and thus limit the odds of an escalating response.
Preventing excessive physical forces is achieved by protecting the rounds, something already have a degree of by being inside an armoured structure, but internal protective elements can be installed to protect each round in its storage rack, or to protect belted cannon rounds in their magazines. This will either defeat a penetrating threat, or at least reduce its energy.

Reducing shock energy is best achieved by using compressible porous structures and laminates. This is easier in transit where bulky packaging can be more readily accommodated than in the very space poor environment of an AFV interior, but even there layers can be placed into barrier structures such as ammunition compartment blast doors to reduce shock wave transmission.
Thermal energy can be reduced by using materials in the munitions and their protective surroundings that are inefficient in heat transference in both fast heating/impact as well as slow heating conditions. Again, with AFVs this tends to take the form of protection around ammunition compartments and magazines rather than specific design elements in the round itself.
Relevance to AFVs
This is The Institute of Tanknology, so what does any of this have to do with AFVs at the end of the day? Consider the short video below, particularly the slow motion footage from 00:25 onwards.
This is a TOW-2B missile firing an explosively formed penetrator (EFP) down through the tank's roof. Note though that though there is a significant fireball as the EFP initiates, it very quickly dies away and there has been little effect yet - the EFP slug has shot down and penetrated the tank's turret, but effects remain limited.
Inside things will not be ideal, there will be momentary heat and pressure from the penetration, and likely spalling too, but shaped charge jet (SCJ) and EFPs can travel straight through a vehicle with minimal effect if they don't hit something important. EFPs are a bit bigger and slower than SCJ so can be a bit more destructive at the cost of penetration depth, but even still, it doesn't assure destruction of target vehicle or crew on its own.
This is a Russian T-72 though, and that means two significant facts that make themselves known about 75 milliseconds later in the footage. First, that T-72s utilise carousel autoloaders that place all the rounds and propellant in a ring at the bottom of the turret basket. Second, that the ammunition carried in this vehicle being tested is not remotely IM compliant and due the the first fact, is densely packed together down there.

Consequently the EFP, or secondary effects from it in the form of fragmentation and heat, have impacted a propellant charge or HE round and it has exploded. A sympathetic reaction has then rolled through the carousel and, confined by the autoloader and the tank structure itself, a very energetic reaction ha developed.
It was not the TOW's EFP that catastrophically destroyed the tank, generating enough force to detach and throw the 12 tonne turret 30 feet feet through the air. That was done by the tank's own ammunition as a secondary effect of the penetration.
IM matters because it mitigates these effects. The nature of large calibre ammunition and the realities of storing it make it certain some king of reaction will occur, but pulling it down from a Type I/II/III into a Type IV/V has a big effect on crew and platform survivability.
Below is another video, this time of an M1 Abrams, showing an initiation of the main charge racks in the bustle. Notice that because the effects are able to vent from the vehicle by virtue of the engineered passive venting blow off panels in the roof of the ammunition compartment, and because although the ammunition burns fiercely with sympathetic reactions clearly occurring through the racks, there is not deflagration or explosion and the vehicle quite quickly burns through available material. Thanks to insulated and armoured blast doors, the inhabited portion of the vehicle is essentially unaffected as can be seen from the internal view in the corner.
Another benefit is that by pulling the response down the severity scale through IM compliance, the chances of controlling or nullifying it with fire suppression systems increases. It is not possible to suppress a detonation with such a system - the reaction is occurring due to a shockwave and so cannot be halted by surface or air treatments. However a burning or deflagration reaction can be stymied or snuffed out as it starts by modern fire suppression systems, which can detect and extinguish a developing fire or blast in less than 100 milliseconds. As such even an outwardly negative sounding Type III response to an IM test can in fact be enough to pull it into a bracket where it becomes quite safe to be located within an AFV compartment.

Bear in mind however the point made throughout - branding something IM does not mean the whole round has a nice green IM Signature matrix. It may just mean a portion of the round is compliant, or even that it is still failing the pass grade, but performs better than another round. For example, the General Dynamics Ordnance and Tactical Systems 120 mm IM HE-T round features, as the name suggests, IM compliant elements. But this refers to the composition of the HE filling in the round, and not the propellant in the case. If subjected to energy whilst in the ammunition racks, it could well still develop into Type I/II/III responses as its propellant ignites, but at least would ensure the HE does not detonate.
Conversely, the Rheinmetall DM63 APFSDS-T round has replaced earlier propellants with a Rheinmetall Nitrochemie Solvent-less, Surface Coated Double Base Propellant (SCDB) that has good IM properties resulting in Type V responses (burning) to BI and FCO tests, Type IV (deflagration) to SCJI (which is very impressive) and Type VI (no reaction) to SR when in standard protective containers.


Concluding thoughts
Responses to IM tests have made great strides in recent years, and the technology undoubtedly has huge benefits. Aside the obvious immediate benefits that it is less likely to destroy a vehicle and kill the crew in the event of a penetration or other incendiary incident, there are implications for logistics and cost that are significant.
Safer ammunition can be transported more densely and with less stringent safety precautions, so is able to be stored and distributed in greater volume, at greater pace and at lower cost. You may also be able to store it more densely and thus achieve a greater 'stored kills' capacity than with non-IM ammunition.
Above all though, is a repeat of the opening quote - "Not 'safe', just less violent" - we are still dealing with explosives, propellant, and various energetic materials specifically designed to do very dramatic and destructive things. IM is about lowering the order of response towards an aspirational NR response grade, but it is not a stamp of safety that means the round is effectively inert, and the odds of achieving NR across all six major threat tests is very, very low.
But, if you can get a round to respond at Type IV or below, and you have some clever design and good fire suppression, you may be able to turn catastrophic loss of life and equipment into a survivable event for all involved and a (probably not insignificant) repair job rather than a recovery of a burnt out hulk.
he protected ammunition compartment is of a Leopard 2 tank