Primer: Powerpacks
- Jon Hawkes
- Jul 15, 2024
- 7 min read
Powerpacks are magical bits of engineering, and vastly underappreciated. Aside from the obvious fact that they are what makes the entire AFV able to move as well as providing it with its electrical power and more, the average AFV pack is a marvel of engineering and a logistical godsend.

For ease of access, I've split this primer into five parts:
Introduction to powerpacks.
The cooling system.
The engine.
The transmission.
Future AFV propulsion.
What is a powerpack?
A marvellous bit of engineering, that's what! More specifically, it is the integration of the engine, transmission, and cooling system (and steering unit, for tracked AFV) into a single cohesive component, fitted with quick disconnects for fluids and power couplings, mounted to a frame that allows it to be rapidly removed from a vehicle in a single piece and placed on the ground without specialist frames or receiving assemblies. A powerpack is also able to be run up for test outside of the vehicle.
Whilst a fully integrated powerpack is a norm on all AFV today, they took some time to formulate into the contemporary configuration.
The concept of a self-contained and rapidly removable engine system was pioneered in the aviation domain, with the Fw 190 fighter's BMW801 radial 14 cylinder engine removable as a rapid integrated component back in 1941.

The British FV300 family, developed between 1947 and 1950 but cancelled after just two prototypes, was the first British AFV to feature a combined engine and gear box with the aim of a quick change powerpack concept, but this would not form a precedent just yet, with most immediate post-war AFV featuring only partially integrated components, generally integrating engine and cooling group but leaving either the transmission, steering unit or both out as separate components.

It is generally accepted that the Leopard 1 and M60 tanks, both developed in the late 1950s and introduced in the early 1960s, were the first in-service AFV to feature the contemporary norm design and configuration of a powerpack, and barring a few odd exceptions has been the only way AFV treat their automotive components since.
Why is a powerpack so important?
What makes the overall concept so valuable? Factors that are most tightly correlated with failures in automotive systems include:
Where the system is producing and transferring a very high power output;
Where the vehicle is experiencing a very aggressive usage profile (particularly hard acceleration, turning and braking);
Where the vehicle is of a very high mass;
Where the vehicle is in harsh environmental conditions.
Those factors are all not just present, but are the norm for an AFV. That means that AFV automotive components break down a lot and need very intensive regular maintenance work. As an AFV is a military vehicle, it needs to be fixed and returned to users fast, and all within austere field-based environments, rather than dedicated workshops with specialist facilities.
The powerpack concept allows mechanics to disconnect and remove the entire pack rapidly (typically in <15 minutes) in one piece, and due to the integrated pack frame it can be placed straight onto the ground.
It can then be worked on with good space and access, and the entire pack can be connected to external umbilicals to run it up for test and inspection to diagnose issues or test fixes without having to refit it to the vehicle.
In the event that a quick fix is not possible, a replacement pack can be dropped in, and the defective pack pulled back for 2nd line maintenance, escalating as required up to shipping it to a OEM for full rebuild.
The impact of such a capability cannot be understated – restoring AFV to service following automotive failure moves from days to minutes, and the efficiency of handling and repairing those systems is radically improved.
Whilst this line-replaceable unit (LRU) approach is quite normal across large complex platforms today, within automotive systems it is still very rare outside of aviation (where it is typically called a quick Engine Change Assembly (QECA).
The Anatomy of a modern AFV powerpack
In broad terms the engine installation in an AFV comprises four main systems:
The powerpack - the engine, transmission and cooling system integrated into a single piece component that can be rapidly fitted to and removed from the vehicle.
The air intake and filtration system that enables the engine to draw in fresh, clean air for combustion. Note this is not the same as the cooling system in the powerpack.
The exhaust system that disperses combustion gases from the vehicle.
The fuel system including pumps, filters and tanks, with the majority of fuel tanks fitted elsewhere in the vehicle and not within the pack.
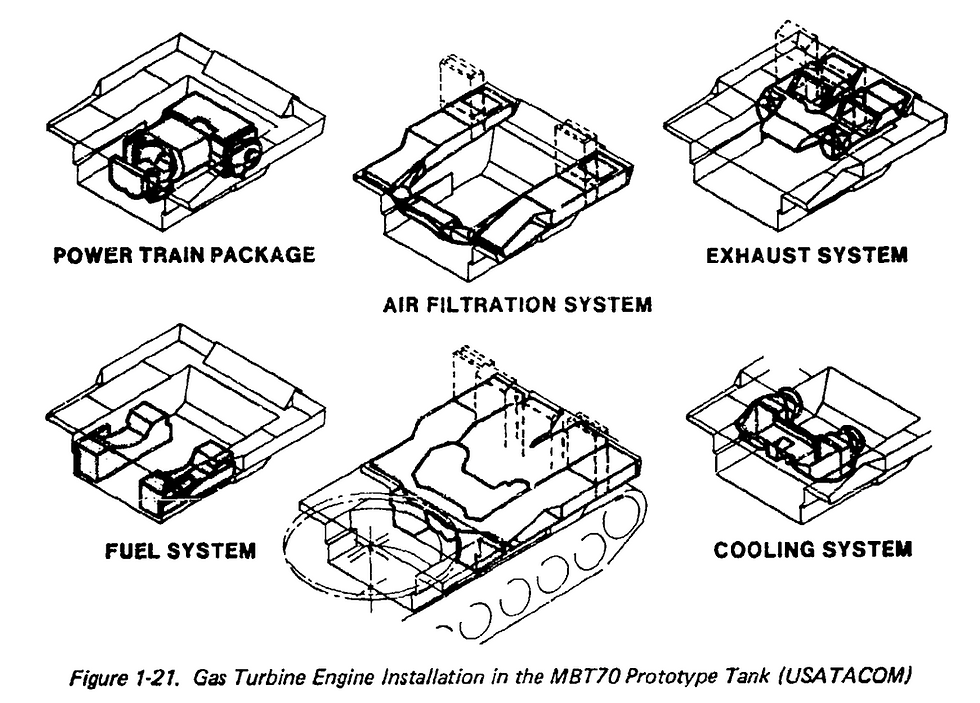
The powerpack itself is an incredibly densely packed integration of engine, transmission, and cooling system. Though by no means simple, the engine and cooling are relatively straightforward and well understood technologies, with the main challenges being around how best to package them. The transmission, however, is arguably the most important component in the system, and more often than not in the AFV as a whole.
AFV transmissions are spectacularly hard to engineer and most brand-new design AFV start with the transmission, then construct a pack for it, and work out from there. It can represent as much as a third of the overall cost of a blank slate tank design, although that figure has reduced more in recent years as the vast array of expensive electronics on a vehicle has increased.
Reflecting the challenges of tracked AFV transmissions is the fact that so few companies are capable of independently developing one. Globally there are less than 10 companies that are capable of manufacturing reliable and capable transmissions at the power and weight class required for a 40+ tonne AFV, dropping to perhaps 5 for 60+ tonne vehicles. Many have tried, and most have failed to join this group, arguably led by Germany’s RENK Group but absolutely including highly capable solutions from the likes of Allison and SAPA, the latter with their mind bendingly complex 32-gear ACT transmissions.
A note on metrics and power losses
When comparing automotive systems it is tempting to focus purely on a Top Gear attitude that 'powarrr' is the most important thing. A 1,200 hp pack is 300 hp worse than a 1,500 hp pack - simple!
But it is not that simple - there are a lot of specifications for an engine alone, including both power (hp/Kw) and torque (lb-ft/Nm), but also much more nuanced factors around load distribution, power delivery profiles and responsiveness of delivery, to name a few.
One factor that is rarely discussed, not least due to a huge paucity of data on the subject in the military domain, is that of power losses. A comparison that two different weight AFV with 1,500 hp packs makes the implicit assumption that 100% of power is being delivered to the tracks, when it is not.
The AGT-1500 in the M1 Abrams, for example, produces 1,500 hp (hence the name). However, the power available at the sprocket is around 1,050 hp - a massive 450 hp, or 30% of the engine's power, vanishes on the way. As power losses are dynamic, this can spike be 50% or higher in certain conditions.
The same sorts of values are true in other vehicles and powerpack designs, there is no way to avoid substantial power losses when passing forces through mechanical interfaces, and there are a huge number of them in an AFV transmission, particularly tracked ones including integrated steering mechanisms and hydraulic torque transfer mechanisms that have substantial lag when spinning up.
Power losses are classified as steady-state and dynamic, broadly reflecting steady speed operation and acceleration/braking respectively.
Steady state losses happen in the transmission torque converter, the transmission oil pumps, clutch packs (where a mechanical clutch is use), drag in seals and bearings, gear windage and friction, and final drive losses.
Dynamic losses include rotational inertial losses from angular acceleration of components in the drivetrain while accelerating the vehicle, requiring all the rotational components like the spinning transmissions, driveshafts and propshafts in the pack to accelerate too. There is also radically higher load and friction within the gears and power interfaces when accelerating load is applied.
Those losses can typically be between 2% (steady state) to 8% (heavy dynamic loading) lost to 'windage' and gear-to-gear interaction, 4% to drag in the clutch pack, and up to 40% to the torque converter depending on the dynamic state of the vehicle (40% reflecting the big losses as the torque converter spins up from a stalled, idle position). There is also around a 4% loss to powering pumps to circulate oil and other lubricants around the vehicle.
There are further parasitic losses through systems that draw on power (mechanical and electrical) from the engine. The aforementioned transmission eats around 15% of the engine's power from mechanical interfaces, and much of that is converted into heat, requiring substantial cooling. Cooling the transmission and engine, plus providing cooling to vehicle electronics and crew compartments typically consumes 10-15% of the available power, and that figure can be higher in the latest AFVs that have much larger and more demanding air conditioning systems than the unconditioned AFV of old.
Why does all that matter? Comparing two vehicle on their input value (hp) alone is a reductive way of comparing vehicles. One may be vastly more efficient at transferring power than the other, or may have radically different cooling, electrical or power-take-off demands than the other. Quite often that difference is a product of the transmission – again pointing to its importance, complexity, and centrality to an AFV automotive system.
Yes, in a 1,200 hp vs 1,500 hp comparison is it very likely the 1,500 hp vehicle has more available power regardless of efficiency, but the gaps may be tighter than expected, and two vehicles of the same power output could have radically differing sprocket power outputs that radically impact other assumptions, such as power-to-weight calculations.
Next...
This is the introduction to a set of relatively short, connected primers, with specific posts coming up for each of the big three parts of a powerpack - engines, transmissions and cooling systems, and finally a general gaze at the future of hybrids, electric and alternative fuel technologies..
Originally these were all part of the one primer, but it was just too big and intimidating, so they've been broken up to be a tad more digestible.
I often hear people bemoan the Challenger’s 1200hp yet I also hear it is faster over rough terrain than many tanks with 1500hp due to the hydro gas suspension.
Also with the likely adoption of unmanned turrets in the near future, do you think we'll see the equivalent of a "turretpack" to ease maintenance on them with their lack of interior access? Given that some designs are physically isolating the turret from the crew and engine compartments, a turret kill might not result in a vehicle kill and could potentially could be replaced relatively quickly.
Do you think electrical drivetrains to electrical motors may be developed, especially with the introduction of electrical power supplies for low signature use?