Primer: Composite Rubber Track (CRT)
- Jon Hawkes
- Jan 17, 2022
- 18 min read
Composite Rubber Track (CRT) is a relatively new method of manufacturing tracks, replacing segmented steel track assemblies with a single continuous 'band' of rubber track, made from a complex composite structure to withstand the tremendous forces involved. Its a remarkable bit of technology and a serious step change for tracked vehicles, bringing with it a range of huge benefits, and has very few drawbacks.
Contents:
How is it made?
Colloquially referred to as rubber band track, CRT is so-named for a reason, with the tracks being comprised of a complex matrix of metals, rubbers, plastics and fabrics to form a single monolithic track with no connections, hinges or other mechanical assemblies. So although the external appearance is of a giant band of rubber, the reality is far more nuanced, complex, and challenging to engineer. A contemporary CRT design designed for AFVs of up to 50,000 kg GVW uses more than 12 separate rubber compounds, with an overall composition of approximately 49% rubber, 29% steel and 22% composites.

CRT is a single-piece track technology, with the entire track being a single continuously cased rubber structure reinforced by a range of composite materials including carbon fibre and carbon nanotubes, as well as longitudinal and lateral steel cords, or ‘belting’. This core belting consists of a single 1,500 m-long steel cord, wrapped about 100 times around the profile of the track. Above and below this belting are multiple layers of steel mesh configured to resist track twisting and maximise the longitudinal torsional stiffness of the track matrix.
The inner surface features a single centre guide lug to maintain the track’s lateral position relative to the road wheels and two drive lugs to ensure good transfer for torque from the drive sprocket to the track.
Each of these components are reinforced internally with the specific design varying depending on the platform’s GVW and intended usage profile, with steel fabric or plastic sheeting, as well as resin and fibre-based stiffener on the surface to ensure even distribution of road wheel load onto the entire track width for best uniformity of ground pressure. This stiffener is also critical in managing heat build-up from hysteresis, with a required tolerance of more than 160°C.
A range of rubber compounds are used throughout the track matrix, with stiffer compounds in the lug cores and softer, more pliable, and UV-resistant compounds on the surface. Those elements, interfacing with moving parts such as the surface of the drive lugs that engage with the drive sprocket, use compounds that have high resistance to abrasion, a low friction coefficient, and are self-lubricating.
Actually making the tracks is a complex affair and one of the key barriers to entry for suppliers. So far, only Soucy seem to have nailed the process to make a high mileage track at the GVW capacity required for a contemporary AFV. Their process sees three key subassemblies manufactured separately, with the rubber produced mainly through extrusion of calendaring then cut to length, stamped, die-cut, reinforced, superimposed and compressed in multi-layer elements.
Once the three elements are ready, they are joined. These are the inside of the track, including the road wheel path and the drive and guide lugs; the external profile that includes the tread pattern that will interface with the terrain; and the internal banding matrix. Once aligned, they are placed in a press to cure into a monolithic track.

Soucy keeps the specifics of that close to its chest, but the technical challenge for companies trying to make CRT is maintaining shape and tension as well as a uniform heating and curing process without adverse impact from metallic components heating and dilating or otherwise expanding, all whilst maintaining a pressure of more than 1,000 psi. Once complete, you have the finished single piece 'rubber band' track ready to be fitted.
Fitting CRT to an AFV is not simply a case of swapping a traditional track for a CRT alternative. CRT is a complete drive system, and requires replacement of the full running gear with specific CRT-oriented parts, including the CRT itself, as well as bespoke sprockets, idlers, road wheels, and return rollers. A bespoke tensioning device is also required. This does require some modest engineering work and can require minor tweaks to the design of the vehicle, particularly where skirts or armour sit outboard of the running gear area and may foul a CRT track.
What's so great about it?
On the surface, CRT appears a like-for-like replacement for metal tracks from a capability perspective, however the differing construction and profile brings with it some significant differences in performance, characteristics and capabilities over conventional tracks.
Automotive benefits
From an automotive perspective CRT brings significant increases in performance when compared to a typical double-pin steel track. In published results of trials conducted in 2018 where a British Army Warrior was fitted with a CRT package and run comparatively over battlefield missions alongside a conventional steel service track equivalent a range of representative data points were revealed.
CRT tracks bring up to 60% weight savings over steel equivalents with the British Army's Warrior trial seeing a saving of 1,502 kg reflecting around 5% of the vehicle's GVW. As the CRT tracks are made from rubber, their weight saving increases when submerged in water, possessing much greater buoyancy than steel. In the case of warrior, it increased the buoyancy a further 29% to almost a 79% overall saving (c.2,300 kg) versus steel.
This increased buoyancy vastly increases mobility in waterlogged terrain where all vehicles struggle to move, and is of special interest to designers and users of amphibious vehicles that would gain additional GVW capacity afloat, or improve their seaworthiness while afloat, as well as make transiting the surf zone far easier.

The weight reduction drives a number of consequent automotive benefits, though the nature of the CRT design also impacts these for a compound effect. A 2016 paper on CRT gives a few more details. Owing to the much lighter weight, the frictional losses in the running gear are up to 50% lower than a steel track, and the fuel consumption falls significantly as the effort to move the track and the vehicle is reduced. This is typically in the 25% to 40% range and is vehicle dependent, though the high end of this range has been proven by operational CV90 fleets and is not simply a best case lab figure. The Warrior trials by the British Army's Armoured Trials and Development Unit (ATDU) over a 5,000 km repetitive battlefield mission cycle showed a 16% fuel reduction on roads and 24% off road, increasing range by 19% and 31% respectively. Combining these figures into a mixed mission profile (25% road, 75% off road) would see around a 28% range increase from 418 km to 534 km. Norwegian trials of M113 with CRT in 2016 showed similar findings, with a fuel saving of 33% and a range improvement of 50%.

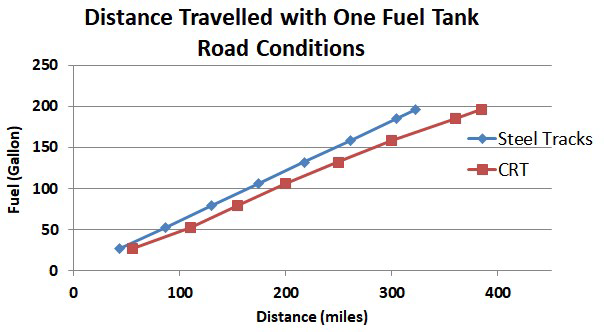
With tracks responsible for the bulk of an AFV's noise and vibration generation - as much as 75% comes from 'track patter' as the tracks interface with the running gear - CRT produces significant reductions owing to its monolithic rubber profile being far quieter than steel in interacting with other components. In broad terms CRT sees 60% and 70% reduction to noise and vibrations respectively. In the case of CRT, the reduction to noise varies depending on where the measurements are being made. Noise reductions are similarly significant when using CRT, with a reduction of 10 db to 15 db.


A secondary benefit of the reduction in vibration is that there are fewer vibrational forces being passed to the platform and on to critical systems. This reduces the demands on the stabilisation and dampening systems in weapon and optical control equipment, increasing accuracy and reliability.

Automotive performance is greater owing in part to the greater contact area, with draw bar pull increasing as much as 191% in normal conditions (this figure reflecting a Norwegian M113A3), rising to 240% with snow chains fitted to the CRT. Stopping distances were similarly improved, with Norwegian Army trials of a CV90 demonstrating a reduction from 330 m to 116 m when braking from to a full halt on ice. Trials conducted by BAE Systems in 2020 with their Mobile Protected Firepower (MPF) prototype saw a stop from 45 mph in two vehicle lengths when on CRT.
The final metric commonly shown as a benefit of CRT from an automotive perspective is that of ground pressure, measured either in MMP or VCI, which typically reduce by around 25% and 20% respectively (24% and 17% in the UK Warrior IFV trials). Lower ground pressure inherently increases other automotive capabilities, including the aforementioned draw bar pull.
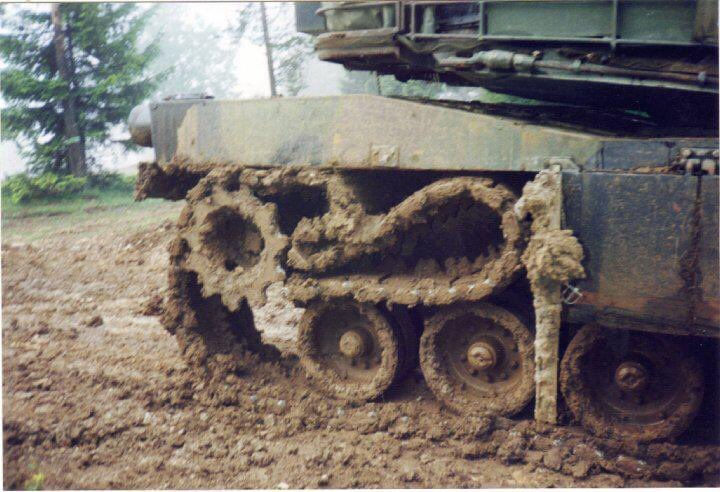
CRT is also much less likely to lose a track, owing to the higher tension it is fitted with. To ensure good fitment, CRT is 30-50% higher than conventional steel tracks in terms of nominal track tension, meaning vehicle movements that might slacken and lose a steel track are less likely to see CRT come off, up 87% less so according to trials data. If a track does come away, it has an inherent tendency to do so inwards from the idler wheel rather than outwards, fouling against the hull and slowing the vehicle. It can often be walked back on rather than having to be refitted from this condition, which is a relatively quick and simple process by comparison. A steel track generally tends to throw outwards from the sprockets, which sheds it entirely and requires it to be broken and fully refitted over a significant amount of time. A CRT modification programme typically fits anti-damage plates to the hull sides to mitigate the effect should a track shed inwards, comparatively unlikely as it may be.
Survivability benefits
One common critique of CRT is that it is less survivable than steel tracks, a not unreasonable assumption borne out of a belief that rubber will be inherently weaker than steel when subjected to blasts, penetration or burning. However, the reverse is generally true, with CRT offering greater survivability in most situations.
Though CRT is predominantly a rubber structure and so at greater risk of cuts and abrasion than steel tracks, the latter are very rigid and so impact more roughly against obstacles where CRT can deform to reduce the shock or stresses. Kevlar fibres are also mixed within the CRT matrix to provide increased resistance to cutting and chipping action.
In the case of blast attack such as a mine or IED, the CRT will again deform to absorb a significant amount of shock from the blast, where a steel track has little to no capacity to deform without failure. CRT can lose chunks of its profile (so called "cookie chunk" damage) and still maintain strength and function where even a small loss of material from a steel track body is likely to see it fail under the stress of use. The benefit also extends to secondary effects of a blast attack. Should a blast disintegrate a track (of any construction method), fragmentation and debris is projected outwards from the running gear. In the case of CRT, this will be comparatively light and soft rubber pieces rather than shards of metal from a conventional track, and so pose much reduced risk to the personnel, equipment and environment around the vehicle.

When subjected to ballistic attack CRT will be penetrated in essentially any instance, however the very high pressure of the rubber structure means that holes are essentially self-sealing as the rubber elements expand to fill the void, where impacts with metallic tracks can credibly cause pin fracture failures or damage bushings. In most cases CRT is relatively unaffected by blast damage unless directly under the track, and Soucy have anecdotes of mine blasts destroying the suspension causing the track to fall off the vehicle, but the track is perfectly fine when inspected, its just everything around it failed.
Finally, there is a commonly held belief that CRT will be more vulnerable to fire and burning than a steel track, based on the relatively logical assumption that rubber will burn and melt where steel will not. however, the composite structure of a CRT track is formed under very high pressure and has very little air within it, resulting in it being very hard to burn. In fact, the rubber bushings of a steel track are likely to fail before CRT would, with consequent failure of the track assembly shortly thereafter. A more significant issue is that a fire heats the track. In CRT, this has little impact, as the bulk of the track is composite and the metallic components - the steel longitudinal cords, will not significantly warp or change the structural integrity of a CRT track. Conversely, a steel track will warp significantly under heating, and can rapidly see pin and other linkage elements fail as they deform.
Logistical benefits
The logistical impact of CRT is perhaps its greatest benefit, and one that isn't as widely discussed as it ought, not least because logistics isn't seen as the sexy topic it should be!
Helicopters have been described as "a million parts rotating rapidly around an oil leak waiting for metal fatigue to set in" and the running gear of an AFV is largely the same paradigm. Hundreds of component parts, all in motion and moving in such a way that a failure of any of them can often be quite dramatic for the system as a whole, constantly hammered with forces in the tens of thousands of kilograms. With all of these parts in motion, including the suspension and roadwheels, the idler, return rollers and sprocket and the many component parts of the track itself, there is a lot of wear and tear, and things need regular maintenance and replacement.
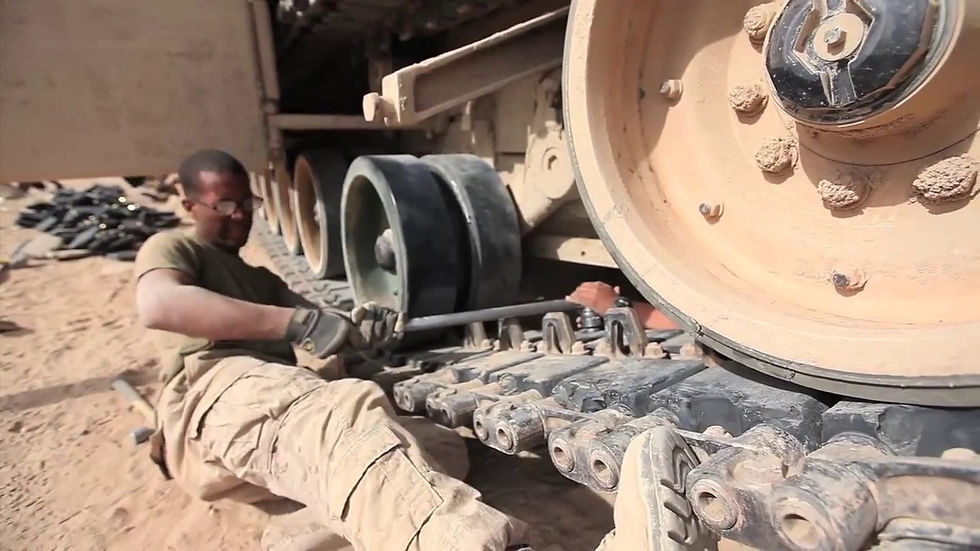
As a result of all of this, conventional steel tracks have a life of around 5,000 km (this can increase or decrease significantly depending on usage profile, but is a reasonable average for a mixed profile without anything too extreme in there). However, this is just the life of the critical element - the link bodies themselves. There are many components within the running gear that age much faster than this and are replaced several times over during the life of a track.
The rubber track pads need replacement every c.600 km, and there are typically over 150 of them on a pair of tracks. The road wheels need replacing every 1,500 km and there are 14 pairs on a tank or heavy IFV. Sprockets and idlers last 2,000 km to 3,000 km. End connectors and pins experience varied wear rates, but can require ad-hoc replacement during the track life. All in all, the life of a steel track may be quoted as c.5,000 km, but in that time you are likely to need to replace 3,000 track pads, 56 road wheels, 4-6 sprockets, 4-6 idlers, the 152 links themselves and 2-6 return rollers. That is a significant amount of space, weight, cost and time. One pad change alone can be 18 hours work for a crew.

Now flip over to CRT. CRT has a typical life for vehicles of up to 55,000 kg (which is the current effective GVW limit) of at least the same as steel. Trials with Warrior and other internal Soucy trials have shown 6,000 km up to a max of 8,000 km can be achieved. So lets be pessimists and say its the same - that's good, we have all these benefits above, with no reduction in life. But the critical bit people miss comes in - the CRT system (the tracks, road wheels, idlers, sprockets and return rollers) is a complete system that is replaced as a set and all has a uniform life span. You install a CRT set onto the vehicle and then do not need to replace, adjust or maintain (other than a daily visual inspection for unanticipated damage) anything until the track is worn out at 5,000 km to 8,000 km. That is part of how CRT saves so much weight - the pads are c.30% of the weight of a track, and CRT has none (or fully integrates them, depending on how you view it).
Steel track also constantly slackens as bushings compress over time, requiring at least daily adjustment. CRT is very rigid by comparison, with no tension adjustment required during its life, as it does not stretch at all.
The logistical, cost and time saving of these factors cannot be understated. You go from continuously adjusting and replacing over 3,250 components to fitting c.24 and leaving them there until the next replacement. With most Western AFV doing very modest mileage in peacetime, the track maintenance becomes just a single task every 3 to 4 years in depot maintenance cycles, and not a daily burden for the life of the crew. The Warrior trial with ATDU cited at least a 415 hour time saving during the 5,000 km trial.
What's wrong with it then?
Well, not much actually. A few common objections or criticisms have already been covered above - blast, fire and ballistic damage - all of which are not as the popular view may expect and actually better with CRT.
Perhaps the key objection that tends to be voiced is around the cultural mindset change to CRT logistics - implications of carrying and fitting new tracks - they are after all quite substantial single piece components of not insignificant weight and a wholly different beast to 'good old steel' tracks. This one is more of a cultural issue, people don't like change and the old guard in the armoured world will cling to their steel as their forebears did their horses. Technological evolution sometimes requires accepting certain compromises to get the benefits.
Fitting a new track is ideally done using some machinery and tooling Ideally the vehicle is lifted either by crane or air bag inflated under the belly, and then the tracks lifted off and on the vehicle by a forklift, which would be entirely viable in the field or in a dedicated maintenance facility.
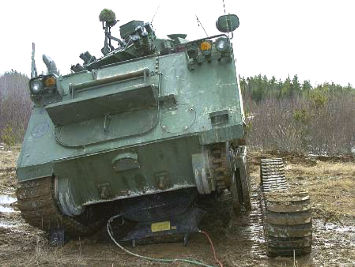
However if the replacement is taking place in austere conditions, a track can be manhandled onto a vehicle relatively easily, in AFV terms at least. During the ATDU trials a swap was carried out in the field, with a team of six soldiers replacing the CRT system by hand in 2 hours 20 minutes.
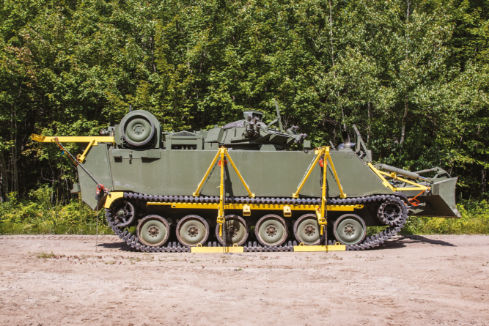
So its no worse, really, its just different. The key thing though is to get out of the mindset of replacing tracks in a field, because 99% of the time you won't need to anymore, that is a false assumption that you will be working on CRT as intensively and frequently as you did on steel tracks.
CRT doesn't fall off easily, it doesn't break easily, it lasts longer and needs no maintenance. Track replacements would almost always be planned events in a workshop and only needed every few years in typical usage. Obviously accidents happen, but in any case it can be repaired or replaced by hand, and with a little creativity it would be very easy to envisage a set of tools to do it quickly even in deployed environments. Think Defence can doubtless give us all a million options for lightweight field machinery to do the lifting and moving that is a little more intelligent than the crew and a wrench.
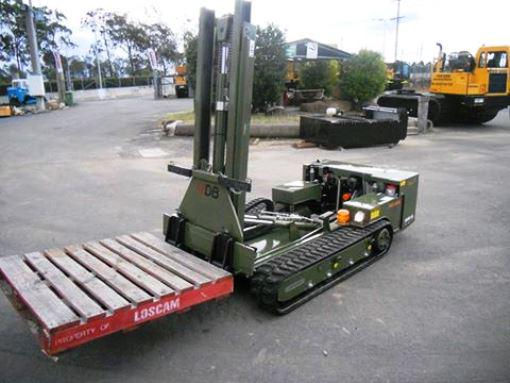
If a track is broken, the options to keep going are a bit more limited than steel. With steel tracks you always have the option to break the links around the damaged area, insert fresh links, and reconnect (though its many hours longer and more stressful than that sounds). CRT is less flexible in this regard. Though less likely to break, it can, and if this happens there are two options, the full replacement mentioned above, or a field repair is possible using a battle damage repair kit (BDR). The BDR rebinds the track and a bit like those skinny tyres in cars these days allows a reduced capability to return to a point where a full track replacement can take place. These kits can be carried on the vehicle and take up less space and much less weight than a bunch of spare track links.

Weight limits are a regular concern - CRT is not able to be fitted to MBT class vehicles still, and this is taken to infer a flimsiness to the technology. Though CRT does have a GVW limit of 55,000 kg, strength is not the issue, heat is. As the weight increases, the heat generated primarily via hysteresis is tremendous, and very hard to dissipate. Ideally the tracks would get wider, and thus have more 'room' to accommodate the heat, but track width is a relatively hard limit due to external logistical limitations, and as most tanks fit heavy skirt armour on the sides of the vehicle, and a wider track would prevent this or force even larger vehicles.


As a result, the tracks are stuck at little more than normal steel track widths - typically no more than 650 mm. With this constraint any GVW increase, which will cause significant heat increases through the track profile, will require the dark art of materials science to devise new compounds to dissipate heat quicker, or prevent its build-up in the first place. Without this mitigation, the heat build-up causes rapid degradation of the track, leading to it breaking up or failing well before a required lifespan. This factor is the key one preventing other suppliers from success in the CRT market - the right mix of chemical and mechanical engineering to create a long life track at high weight is a significant challenge.
That said, the pace of GVW increase has been remarkable. A few years ago Soucy said the max was 40,000 kg and could not envisage it ever reaching MBT classes of 55,000 kg and higher. Yet barely 3 or 4 years later, they have 55,000 kg class CRT. So while this remains and issue for tank fans, it may not forever. Getting much past 60,000 kg without a track width increase feels unlikely, though. That said, if next generation MBT integrate CRT at the design stage, larger tracks could be accommodated and this barrier broken.
There is often an objection that CRT must cost a fortune, given its complexity and 'newness'. Current CRT tends to be about 10% more than a steel track to buy as a single 'set'. But that can reduce or even invert as you move into more specialist tracks - some lightweight tracks for vehicles like Ajax or Lynx cost more than a CRT system would have cost. But in general if you can field good old steel tracks, then CRT will cost a bit more, at least for now. However that's a one time purchase cost, not a through life cost. The reduction not just in primary costs of the many spares during the life of a track, but the secondary and tertiary costs of storing, moving and fitting them are huge. Hundreds of logistics vehicles do not need to make journeys to maintain the massive tail of armoured formations if they have CRT. A comprehensive study of the whole life cost saving has yet to be published, but data from users of CRT suggest a 20-25 year vehicle life cost saving of CRT is at least 40% in spares alone, with fuel savings to be added on top. As always with kit, the purchase price is not the bit to focus on for efficiency and savings, its the operation element, and CRT is very attractive there.

Finally, a few commentators voice understandable concerns around extreme temperature operation - does CRT become brittle in the arctic or melt in the desert? No, it is stable in these conditions as has been used operationally in Afghanistan as well as domestically by most of the world's coldest users in Scandinavia. The same rubber compound is used in all climates, without a need to swap to "warm or cold weather tracks" as might be expected.
What alternatives are there?
In a like for like sense, not many - the barriers to developing a high mileage life CRT system have so far proven sufficient to prevent anyone but Soucy fielding a solution in the weight classes required for modern AFV, which is typically 30,000 kg to 50,000 kg GVW.
The successful design Soucy have made seems to be a very challenging success, with competing attempts at a monolithic CRT having largely failed, usually due to low mileage with attempts often resulting in tracks that break up rapidly after c.1,000 km. The barrier to entry is also quite high - the speciality manufacturing equipment, particularly the high pressure curing presses for assembling the final track, are enormously expensive and represent a huge investment for a company to make when it cannot assure success.
The majority of alternatives therefore are other technologies - segmented rubber/band track, and lightweight metal track. Both will be covered more in separate posts in the future.
Diehl are perhaps the most prominent defence player in these adjacent domains. They make a number of segmented rubber track (SRT) (or segmented band tracks (SBT) solutions, but SRT is quite different to CRT. By its nature SRT is segmented - typically a single connection but with designs available that feature a number of separate segments that are connected together. This means the core strengthening elements of CRT - the longitudinal cords and the monolithic cured rubber encased structure - are not present, and as a result SRT is significantly reduced in longevity, GVW capacity and strength, limiting their use to lighter vehicles are reducing their relative advantage over conventional metal track designs. There are appeals to SRT - it could be stored and transported easier, and fitted more readily in austere conditions. This has led to a programme in the US for an SRT solution for the MPF light tank, but in general users recognise the value of CRT and show broad preference for that technology.
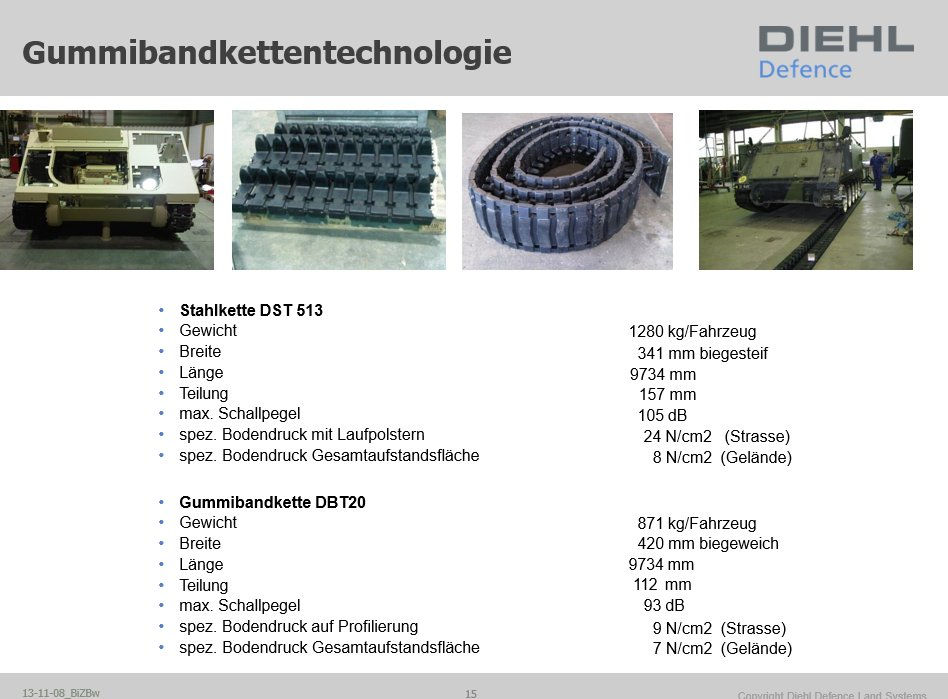
Diehl are also significant in the lightweight metal track market (alongside other well-known suppliers like William Cook). Lightweight tracks try to reduce track weight for AFV that are close to their GVW limits by utilising lighter materials and/or 'stripped down' construction methods to reduce mass. In an age of SRT and CRT they generally are a poorer (and often more expensive) option, being heavier than the rubber alternatives and often bringing a range of undesirable characteristics like increased noise and vibration. They nonetheless remain an option for users when dealing with weight issues in the running gear.
There are a lot of rubber tracks in the agricultural sector, where dedicated or retrofitted track systems for tractors and other vehicles are increasingly the norm, where they offer reduced ground pressure than wheels resulting in better tractive mobility and reduced soil compaction. However, the weights involved are generally lighter, and the usage profile radically different. Agricultural vehicles wish to disturb and compact the ground the least amount possible, so make gentle movements, the vast majority of which is slow and in stead paths. Forces exerted on the track are largely limited to the longitudinal axis with lateral and twisting forces comparatively low.

AFVs, by comparison, do a lot of harsh acceleration, braking and turning. The impact on the terrain is largely irrelevant, with the sole goals being terrain access and fast effective movement. As such agricultural rubber tracks are far less complex and would not sustain an AFV usage profile, rapidly breaking up or overheating (and then breaking up). So there is limited crossover and relevance for these manufacturers and a significant engineering and cost burden to make the move up into the defence market.
The future
Clearly CRT is pretty impressive stuff, and though considered 'new' has been fitted to operational AFV for decades now. The tech is moving at quite a pace having increased from a maximum GVW of 40,000 kg only a few years ago to 55,000 kg today. Whether it will ever be able to tolerate 75,000 kg or more to accommodate the contemporary MBT is debatable, but never say never given the pace of development. Certainly it looks like 60,000 kg will happen soon, and that would accommodate the projected (or at least desired) weight class of the next generation MBT designs, which hope to be a little lighter than the behemoths of today. While CRT remains a one horse race there is a huge market that Soucy may be hoovering up around the world, and hopefully this value drives some competition in the market to further stimulate development, though to be fair, Soucy seem to be doing very well on their own so far.
If there is a key takeaway, its the suggestion that if your AFV is within the GVW limits there is no overt reason not to adopt CRT technology, its a rare game changer tech with essentially zero negatives and some huge positives to be snapped up.
Disclaimer | As mentioned, CRT is a technology that is essentially produced only by a single company - Soucy Defense. As such, the post could be construed as a bit of a massive advert for Soucy, which is not the intent. CRT is a wonderful capability and a technology that, I think, should be a default choice if your vehicle is within its specifications. For now at least that means Soucy should make tracks for everyone, and they're to be applauded for their remarkable achievements. But to be clear I am not paid or otherwise incentivised to be such a big fan of CRT, or Soucy or anyone else that emerges as a CRT supplier in the future.
Any thoughts on trialing composite tracks on the Ajax program to help with excessive noise/vibration reduction