FFG's Armoured Recovery Module (ARM) for Boxer
- Jon Hawkes
- Jan 17, 2022
- 3 min read
TLDR: The Boxer design concept of distinct drive and mission modules is a cool bit of tech, as I'll cover in more detail soon and profiled on Twitter a while back. The ARM module from FFG is an example of why that approach is great, with a company that otherwise wouldn't offer a vehicle variant having produced a hot-swappable ARV/ARRV capability to nay Boxer user. It adds a lot of capability to Boxer formations, and the self fitting trick is a neat one.
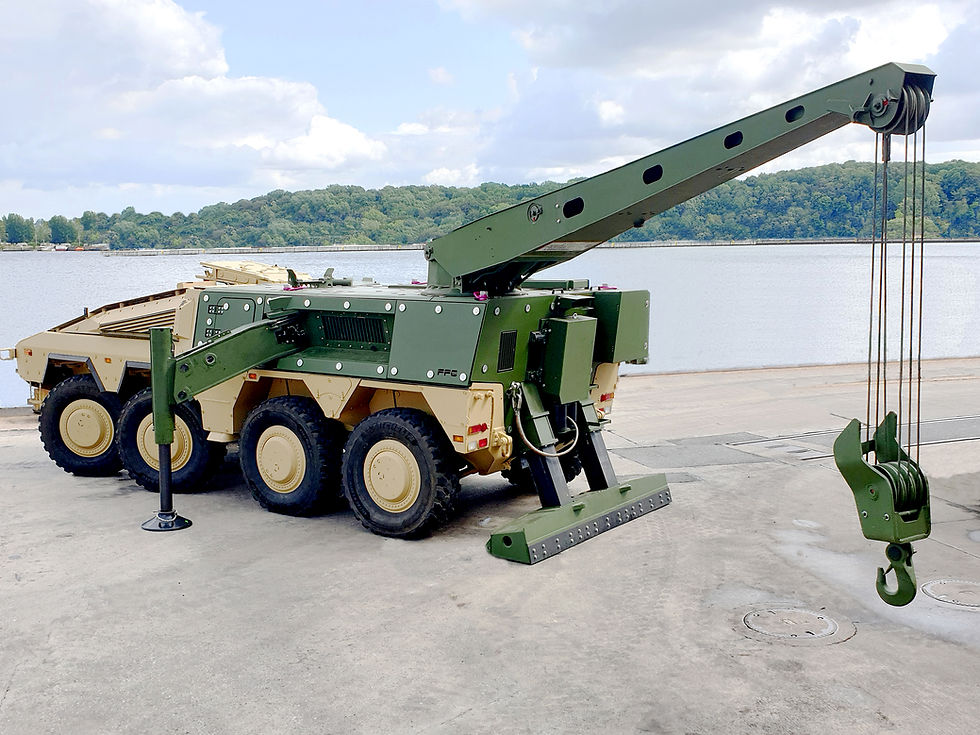
The ARM module is pretty straightforward - a repair and recovery configured mission module weighing 13 tonnes that can be added to any Boxer drive module, mounting recovery winches and a crane. Crew of three - the driver in the drive module, with a commander and gunner in the ARM module itself in a compartment at the front, accessed through a hatch on the front left of the ARM module.. The latter controls an RWS on the rear of the roof, which can be any of the many COTS RWS solutions with a range of armaments..
Recovery gear is a 200 kN capstan winch with a 60 m cable, which is inside the module and plays out through the hatch at the rear. The crane arm is also a 200 kN capacity with a 4 m reach and 6.3 m max lift. All pleasant stuff. Note that these metrics allow for it to lift other Boxer mission modules and thus be used for deployment and maintenance of Drive and Mission modules in the field. Given Boxer must be split into its separate Drive and Mission module components for transport in the A400M, the ARM would offer the ability to first mount itself onto a Drive Module at the destination, then be used to mount further variants as they arrive, which makes the whole narrative a bit smoother and offers some good options.
To provide some stability, it has outriggers at the sides which retract into the Module body for now excess width when stowed, and an earth anchor blade at the rear. Standard stuff for an ARV/ARRV. Note that though the outriggers extend via power controls, it requires manual insertion and securing of the stabiliser feet, which is fine, if not quite as cool as it could have been. Then again, simplicity beats unnecessary complexity in design.
The hydraulics powering the winch and crane are actually powered from batteries in the ARM module, which is charged by the main vehicle power supply. That means the system can run with main engine off, or for a real party trick without a drive module at all, for some reason that isn't immediately obvious. It then has a bunch of pleasant engineering bits and bobs - welding and cutting station, external powered tool connections and so on.

All in all a very handy tool and one that is a fairly obvious addition to Boxer users over a disparate platform ARV/ARRV. If nothing else, a great demonstration of how a supplier can provide a specialised capability affordably without having to get lost in the horrendous time and money pit that is developing a full AFV platform. Here's hoping to more neat Boxer variants in future.
Finally, the UK look to be the first customer, with 102 planned for the fleet (under the name Repair & Recovery Vehicle (RRV)), which is quite a big slice (13%) of the overall UK fleet. These replace the original plan for 60 Engineer Section Vehicle (ESV) and 50 Engineer Support Carrier (ESC) variants that were to be the recovery and repair capability for UK Boxer, but really were just lightly modified APCs. A few of each of those remain in the order to support the RRVs with extra kit and bodies.
Disclaimer | These are posts purely about kit I think is interesting to me for various reasons. I'm not paid or otherwise incentivised to write about these things, I have no affiliation to the organisations and they just happened to catch my eye. I'm interested in the technology and the capability, not the company or the specific system itself.
Is the Boxer module an open standard or do you have to get it compatibility validated by someone (ARTEC?)? Do you think we’ll see armour manufacturers build bare-bones modules for others to fit out with say signals/EW gear?